多物理场耦合干扰电磁-热-力耦合效应导致主轴漂移:数学表达复制下载ΔX=α·ΔT+β·F/m+γ·B²(α:热膨胀系数,β:力变形系数,γ:电磁致变系数)实测案例:某高速主轴在40,000rpm时,电磁干扰引起位置检测误差μm。三、运维成本与复杂度全生命周期成本高高尚电主轴购置成本占整机25%~40%,维护费用占比:项目成本占比轴承更换45%动平衡校准20%密封系统维护15%传感器更换10%维修专ye性要求主轴轴承预紧力调整需±5N精度操控,非专ye操作可能导致精度长久损失30%以上。能耗峰谷问题主轴加速至30,000rpm需消耗15kW·h能量,占单次加工循环总能耗的60%。四、应用场景局限性重载加工能力不足电主轴持续扭矩通常<500Nm,加工高强度钢(σb>1,200MPa)时金属去除率80cm³/min,比齿轮传动主轴低65%。极端环境适应性差在湿度>80%环境中,主轴绝缘电阻下降速率加su3倍,电机绕组寿命缩短至1,500小时。微型化技术瓶颈直径<1mm微型主轴输出功率限制在50W以内,无法满足硬质合金微钻加工需求(需≥100W)。 辊主要分为以下几类按轧机类型分类型钢轧机辊:用于轧制型钢。浙江辊涂胶轴公司
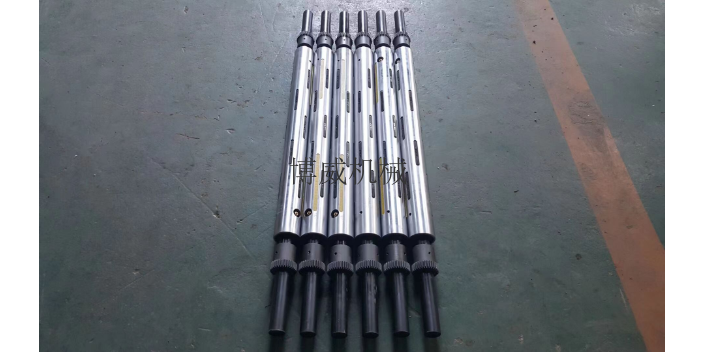
设计目标:•比较大化刚性和抗变形能力;•优化载荷分布,避免应力集中。设计目标:•保证表面质量与轧制精度;•适应频繁更换需求(如磨损后修磨)。3.材料与制造工艺支撑辊工作辊材料选择:•高强度合金钢(如70Cr3Mo、86CrMoV7);•常采用复合铸造技术(外层耐磨合金+芯部韧性材料);•内部韧性要求高,防止断裂。材料选择:•高硬度工具钢(如高速钢、高铬钢);•冷轧辊常用渗碳钢或表面镀铬;•热轧辊需耐高温合金(如半高速钢)。热处理工艺:•整体调质处理(芯部韧性+表面适度硬化);•表面硬度较低(HS55-70)。热处理工艺:•表面超硬化处理(感应淬火、激光熔覆);•表面硬度极高(热轧辊HS75-85,冷轧辊HS90+)。4.使用与维护支撑辊工作辊寿命:•寿命较长(数年),但需定期检测内部缺陷;•失效形式多为疲劳裂纹或芯部断裂。寿命:•寿命较短(数周至数月),因表面磨损需频繁修磨或更换;•失效形式为表面剥落、划伤或热裂纹。维护重点:•监测内部应力与裂纹(超声波探伤);•修复需大型磨床恢fu辊形。维护重点:•定期磨削表面以恢fu精度;•表面镀层修复(如电镀硬铬)。5.应用场景支撑辊工作辊•用于轧机辊系的外侧(如四辊轧机的上下辊)。 铝导轴厂家钢辊原理及应用1. 刚性支撑 应用:用于轧机、印刷机和涂布机等设备,确保材料均匀受力。
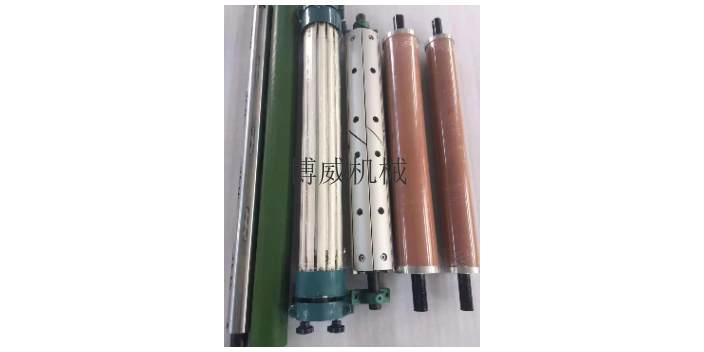
安装方式:固定式(两端法兰固定)、可调式(螺纹或气动调节位置)。同心度与跳动公差:高速场景要求跳动≤,避免材料跑偏。4.环境适应性工作温度范围:常规辊:-20℃~120℃;高温辊(陶瓷涂层):可达400℃。防腐蚀性:不锈钢或表面镀层(如特氟龙)适用于潮湿、化学环境。密封设计:防尘防水(IP54以上)延长轴承寿命。5.其他参数重量:影响设备负载和惯性,铝合金辊比钢辊轻30%~50%。动平衡等级:高速场景需达到(普通)或(精密)。定制功能:加热/冷却辊(温控材料)、导静电辊(祛除静电)、带传感器(监测张力)。选型建议明确应用场景:如输送系统、印刷机、薄膜生产线等。计算负载与速度:结合材料张力、线速度(m/min)和加速度。环境匹配:高温、腐蚀性环境需特殊材质或涂层。维护成本:选择易更换轴承或模块化设计的辊体。
液压轴的名称源于其工作原理和结构特性,主要与液压技术的动力传递方式及机械部件的功能设计密切相关。以下是其名称来源的具体原因分析:一、“液压”的由来:依赖液体介质的动力传递流体动力学的重要原理液压技术以液体(通常是油或水基液体)为动力传递介质,通过密闭系统中的压力变化实现能量转换。例如,早期的液压机通过液体压力推动活塞产生巨大压力,用于锻造或举升(如网页6提到的1925年液压汽车举升机即基于此原理)6。液压轴的“液压”一词直接体现了其依赖液体压力驱动的本质。与机械传动的区别相较于齿轮、链条等机械传动方式,液压传动具有更高的功率密度和精细操控能力。例如,博世力士乐的CytroForce伺服液压轴通过闭环操控液压油流量,实现gao效能动力输出,其“液压”特性明显区别于传统电动或气动轴3。二、“轴”的指代:结构与功能的结合线性运动的重要部件液压轴通常指代液压缸(HydraulicCylinder)或液压马达中的运动部件,其重要功能是输出直线或旋转运动。例如,网页3中提到的伺服液压轴通过油缸的往复运动实现精细定wei,这种线性轴结构是液压系统的典型应用3。 橡胶辊与其他辊的区别5. 维护与寿命金属辊:需防止表面生锈和磨损,定期进行表面处理。
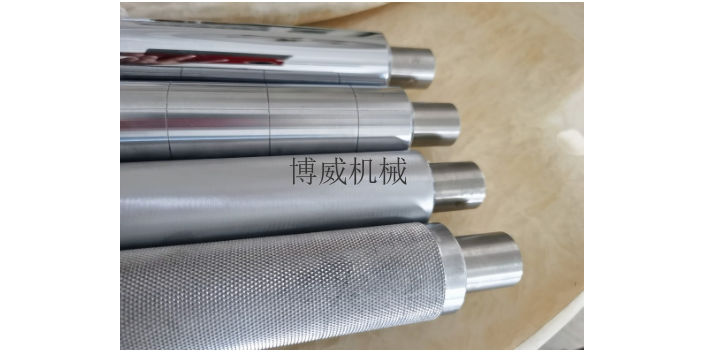
三、加速新兴产业发展新能源行业爆发光伏领域:多线切割机主轴实现硅片厚度从200μm降至150μm,光伏电池成本下降20%,推动全球光伏装机量突破300GW。电动汽车:高速主轴加工电机转子叠片效率提升3倍,助力年产百万台电机产线落地(如特斯拉4680电池生产线)。半导体国产化突破国产超精密主轴(如北京精雕)应用于碳化硅晶锭切片设备,打破日德垄断,使国产碳化硅衬底成本降低40%。四、促进产业智能化升级数据驱动制造智能主轴集成振动、温度传感器,实时监测刀ju磨损(如马波斯测量系统),减少yi外停机70%,并通过AI优化加工参数(进给速度动态调整)。柔性制造支撑模块化主轴设计(如HSK快换接口)支持快su切换加工任务,满足小批量、多品种生产需求(如医疗器械定制化加工)。 压延辊的制造工艺10. 终检 运行测试:进行实际运行测试,确保性能达标。浙江辊涂胶轴公司
特氟龙铝导辊的制造工艺表面预处理 抛光与清洁:对辊筒表面进行抛光处理,去除毛刺和杂质,确保表面光滑。浙江辊涂胶轴公司
3.热处理适应性调质处理:中碳钢轴通过调质可获得良好的综合力学性能(高尚度+韧性)。表面硬化:通过渗碳、氮化或高频淬火,可提升表面硬度和耐磨性,同时保持芯部韧性(如齿轮轴)。经济性高:热处理工艺成熟,成本低于合金钢。4.耐腐蚀性易生锈:碳钢耐腐蚀性差,在潮湿或腐蚀性环境中需表面防护(如镀铬、发黑、涂防锈油)。不适用于严苛环境:长期接触水、酸、盐等介质时需改用不锈钢或进行特殊涂层处理。5.成本与适用性成本低廉:碳钢价格远低于不锈钢和合金钢,适合预算有限或大批量生产。宽泛适用性:常见于通用机械、汽车传动轴、机床主轴、农机设备等中低载荷场景。6.局限性高温性能差:长期在高温(>300℃)下易氧化,强度和硬度明显下降,需换用耐热钢。低温脆性:低温环境下韧性降低,易发生脆性断裂。重量较大:密度较高(约g/cm³),轻量化需求场合需换用铝合金或复合材料。总结碳钢轴的重要优势在于性价比高、加工方便、力学性能可调,适合大多数常规工况。但在耐腐蚀、高温、轻量化或极端载荷条件下,需选择合金钢、不锈钢或特殊材料轴。设计时需根据载荷、转速、环境等因素综合选材。浙江辊涂胶轴公司
文章来源地址: http://jxjxysb.dzyqjjgsb.chanpin818.com/bzsb/qtbzsb/deta_27458141.html
免责声明: 本页面所展现的信息及其他相关推荐信息,均来源于其对应的用户,本网对此不承担任何保证责任。如涉及作品内容、 版权和其他问题,请及时与本网联系,我们将核实后进行删除,本网站对此声明具有最终解释权。